A representative survey commissioned by the digital association Battle highlights the importance of digital applications for more climate protection. According to this, 8 out of 10 companies (81%) say that Industry 4.0 contributes to sustainable production. Around 550 industrial companies in Germany with 100 or more employees were surveyed.
In the course of the survey, 91% emphasized that Industry 4.0 is essential in order tointernational competition to be able to survive. 6 out of 10 companies say that work less error-prone will (61%) and themselves conventional business models will change (58%).
Image: Bitkom
“Through consistent digitization, German industry can face two urgent challenges at the same time: Digitization makes companies more sustainable and competitive.”
– Christina Raab, member of the Bitkom Executive Committee.
Bitkom study “Climate effects of digitization”
The digitization of industry offers great potential Reduction of CO2 emissions. So, in 2030, at a accelerated use of digital technologies in Germany alone up to 64 million tons of CO2 are saved – that is 17% of the total planned CO2 savings as part of the climate target for 2030. This is shown by the Bitkom study “Climate effects of digitization”.
So he can Use of digital twinsi.e. the simulation and optimization of physical products or processes, Save 33 million tons of CO2. Another 31 million tons can go through increased automation in production be avoided by using digital technologies manual intervention and reduce the use of materials such as optimize processes.
“Industry 4.0 has arrived in the manufacturing industry.”
– Christina Raab, Battle
65% of industrial companies with 100 or more employees to use currently special applications for Industry 4.0 and another 25% the plan the use. All in all put 90% of the companies Industry 4.0 – and invest around 6% of their total annual turnover.
Last year According to Bitkom, there were 83% even less, in 2019 were even first 74 %. Only 8% are currently not planning an assignment special applications, but can imagine doing this in the future. For without exception at of the companies surveyed Industry 4.0 is a topic today.
“The corona pandemic has given German industry a lasting boost in digitization”
– Christina Raab, Battle
Every second company (50%) now uses digital marketplacesto buy or sell products and services. A further 17% plan to do so Entry into e-commerce in the coming 12 months and 12% no concrete plans yet, but discuss it. For every fifth company (20%) are digital marketplaces however, not an issue.
Virtual und Augmented Reality is already in 31 % of the companies in action19% are planning this and 16% are discussing it.
Of the 5G mobile communications standard is in 29 % of the companies used and is planned for a further 21%. For just as many (21%), the use is still open for debate.
Lifecycle Management – be there all relevant information about a product managed and made available – every fourth company uses it (25%), more than one in six (18%) plans to use it and a fifth (21%) at least discuss it.
Study looks at the use of artificial intelligence in industry
In almost 4 out of 10 companies (38%) has Artificial intelligence Application found – 66% of them use AI in production to the automation of processes64% for the Data analysis in process monitoring35% turn both uses an.
Concrete plans for the use of AI 17% of the companies have it, 18% are discussing it. For one in four (25%), AI is not yet an issue. The biggest Obstacle to the use of AI see 42% of all industrial companies in the lack of data basis. 40% seems that Effort, especially during implementation too high, 36% lack standards and 32% hinders the certification process. Well every fourth company (28%) gives ethical reasons as a hurdle when using AI.
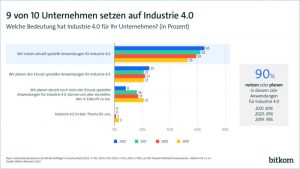
Image: Bitkom
Study results on the use of the digital twin
digital twins are used in every third company (33%). Another fifth (19%) plan to use it and 16% are discussing it.
Raab on this: “Digital twins are digital copies of real-world objects – from products and machines to entire factories. Thanks to their help, Massively accelerate production and maintenance processes and continually optimize it in day-to-day use.”
The importance of digital twins will continue to increase in the medium term. So is a large majority of companies (82%) think that the Use of digital twine in the den increase in the next five years becomes. Only 17% assume that the relevance will not change.
Not a single one of the companies surveyed assumes that digital twins will not play a major role in the future. Nevertheless, for 3 out of 10 (29%) the use is currently not an issue. As with the use of AI, most of them (51%) not enough data availableto deploy digital twins. 38% lack standards and for 23% of all companies, the Profitability cannot be assessed.
Potentials of IoT platforms
IoT platformswith which data, products, machines or processes networked can become use 35% of manufacturing companies and almost as many (30%) plan to do so. For only 14%, IoT platforms are not an issue, for 19% their use is under discussion.
Almost every second person (49%) sees them greatest potential with so-called remote monitoring – i.e. remote monitoring – and with real-time insights into the manufacturing processes. 42% appreciate the acceleration of processes.
39% see potential in the Predictive Maintenance. That’s what they’re called predictive maintenance of machines and systemswhere, for example, parts are only replaced when necessary and then in good time, before a defect occurs.
IoT platforms also help with that Achievement of overarching operational goals again increase in sales (40%), the quality improvement (36%) and the cost cutting (31 %).
“IoT platforms connect products, machines and people in industry and thus drive digital change.”
– Christina Raab, Battle
Raab: “Plants can be centrally monitored remotelydata is available in real time, Processes are automated away. So companies can quickly respond to changes and costly failures through predictive maintenance avoid proactively.“
Specialists benefit from Industry 4.0
The increasing use digital technologies in the industrial environment also changes the job market. 7 out of 10 companies (71%) expect that Industry 4.0 new jobs for well-trained specialists develop. Only 57% said this in the previous year. The industry is now preparing for this change.
More than three quarters (77%) of industrial companies invest in continuing education of their employees around Industry 4.0 (2021: 68%). At the same time, 61% also think that Jobs for the low-skilled will disappear will.
“In Industry 4.0 there is room for employees of all levels of education.”
– Christina Raab, Battle
Raab: “Digital technologies can help to facilitate work in the factory. With the help of augmented reality glasses, for example, you can too Less qualified employees carry out demanding tasksby providing guidance from more highly qualified colleagues or remotely supported on site by software will.”
Accordingly, around half of the companies (51%) assume that complex tasks thanks to Industry 4.0 rather low-skilled workers can be taken over. And 9 out of 10 companies (91%) expect that physical stress in the factory about through the reinforced use of robots further lose weight becomes.
Medium-sized companies have some catching up to do in Industry 4.0
After all 39% of German industrial companies see themselves as Industry 4.0 pioneer. On the other hand, every second person (51%) groups themselves as laggards. 7% of companies feel left behind.
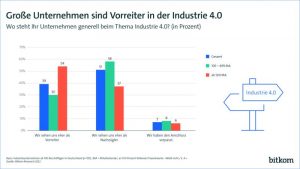
Image: Bitkom
Medium-sized companies have the greatest pent-up demand. 58% of companies with 100 to 499 employees describe themselves as laggards and only 30% as pioneers. The opposite is true among large companies with 500 or more employees: Only 37% see themselves as laggards, more than half (54%) as pioneers.
The biggest Obstacle to establishing Industry 4.0according to the companies themselves lack of financial resources (81%). But also the Data protection requirements two-thirds (67%) perceive it as an obstacle. 61% identify requirements for the IT security as a problem and for 58% it is topic too complex.
Around half (51%) sees in missing skilled workers an obstacle, 4 out of 10 companies (40%) criticize the Interference of systems. 29% is missing the exchange with companieswho face similar challenges.
“The future is industrial business
almost 100% digital.”
– Christina Raab, Battle
In contrast, only a minor role is played Lack of external advice (12 %), lack of knowledge of best practice solutions (12%) or one insufficient availability of marketable solutions (12 %).
Just 6% complain about a too low acceptance in the workforce. “According to their management, every third company (32%) simply has no time to deal with digitization,” says Raab.
More regulation, more funding, more educational opportunities
On the companies’ digital wish lists stand tax measures at the top. 84% call for tax incentives to push investments in Industry 4.0. A similar number – 82% – wish more legal certainty when exchanging data with other companies.
44% advocate the Establishment of standards for Industry 4.0 applications.
“Digitization is the key to the competitiveness and sustainability of German industry.”
– Christina Raab, Battle
About 6 out of 10 companies want one Faster approval process for funding applications (61%) and more than half (52%) advocate the Expansion of R&D funding programs for universities and research institutes. In education, 59% would like Continuing Education Offers and the Integration of Industry 4.0 topics in education and study.
55% want Programs for the training and further education of specialists around Industry 4.0 and about as many (54%) more Information and consulting services for companies.
Bitkom publishes digitization radar as a compass in I 4.0
Bitkom wants to create a clear view of the jungle of Industry 4.0 with a new “Industry 4.0 digitization radar”. It shows relevant technologies and fields of application. As a compass and advisor, it should show which applications are important for Industry 4.0 and what potential they hold.
The digitization radar is continuously expanded and updated. It is aimed in particular at medium-sized companies in the manufacturing sector – and everyone who deals with Industry 4.0. (eve)
–