A universal tool is a useful thing, but it will not be ideal for specific tasks. It is not for nothing that popular wisdom says that what is good for everything is good for nothing.
Car engineers and designers do not lack imagination these days, but their ability to create absolutely universal technical solutions also has limits. And although the electrification of transport is not an overly difficult task, the models created on the new specialized platforms are superior in every way.
We have welcomed the new generation of electric cars
The first electric cars were distinguished by their appearance, but their technical advantages really came to light in the following generations, which were produced on specially developed platforms. Their creation took some time, as a new type of drive and related technologies required significant investment and thousands of man-hours. Even automotive giants like Volkswagen took a long time to develop the ID.3, which was presented in 2019.
General Motors already had an advanced electric car platform at the time, and Tesla and Nissan, which already had products and facilities, were soon joined by Hyundai and Mercedes-Benz. Many electric car manufacturers, such as BMW, still use custom universal platforms or ones designed for both electric and hybrid powertrains. However, most of these companies have already announced that they plan to introduce specialized platforms and even named deadlines.
Jons Vanags, assistant professor of the Faculty of Electric Power and Electronics of the Kaunas University of Technology, notes that electric car technologies have been developing very rapidly in recent years. A good example is the Nissan Leaf. In the first generation models, the synchronous electric motor and current converter were installed separately, but in the new ones they are integrated into one unit.
It may be more difficult to repair such a machine, but when you consider the reliability of the electric drive, it is a huge step forward. In addition, the connection between the various components has improved, there are more sensors, and accordingly the control has become more precise.
Jons Vanags, assistant professor of the Faculty of Electric Power and Electronics, Kaunas University of Technology
Design adapted to electric drive
Specialists inevitably had to change the design of the car, as the previously used platforms were adapted to internal combustion engines, transmissions and fuel tanks. The most important element of the electric vehicle is the battery built into the bottom, so everything had to be changed, including the proportions of the body.
Considerable work has been done not only by body constructors and designers, but also by material scientists. Also, the contribution of electrical engineering and electronics engineers and other specialists is particularly important. In this sense, the fact that some electric car parts are also produced in Lithuania is very pleasing.
Jons Vanags, assistant professor of the Faculty of Electric Power and Electronics, Kaunas University of Technology
If we talk about fundamental differences, then the most striking are two. The first is the abandonment of the central tunnel, which used to be necessary for the transmission and exhaust system. And the second – moving the front partition forward – closer to the wheels, which made it possible to significantly expand the cabin. Volkswagen engineers used it wisely when developing the ID.3 hatchback, while the Hyundai Ioniq 5 is one of the best examples of the new benefits.
On the one hand, engineers and designers gained more freedom of action, but they were working in a new field, and the optimal placement of body and drive elements still required quite a bit of effort. An electric car must be resistant to shocks, compressive forces and various overloads. And each aspect requires specific solutions.
Jons Vanags, assistant professor of the Faculty of Electric Power and Electronics, Kaunas University of Technology
One of the most interesting developments during the development of electric transport platforms was the return to classic or rear-wheel drive. Due to the high torque of the electric motor, the front wheels may start to slip undesirably. During rapid acceleration, the rear axle is more loaded, so the classic drive is more efficient. So it’s no wonder that a large number of new electric cars, including the Hyundai Ioniq 5, Kia EV6 and Honda e, have direct rear-wheel drive.
Recycled and composite materials are used
Due to the battery, the lower part of the car has also changed – it has acquired the shape of an almost regular rectangle, and from below the new electric cars resemble a skateboard. Such a simple configuration also allows you to easily change the number of battery blocks and, accordingly, its capacity.
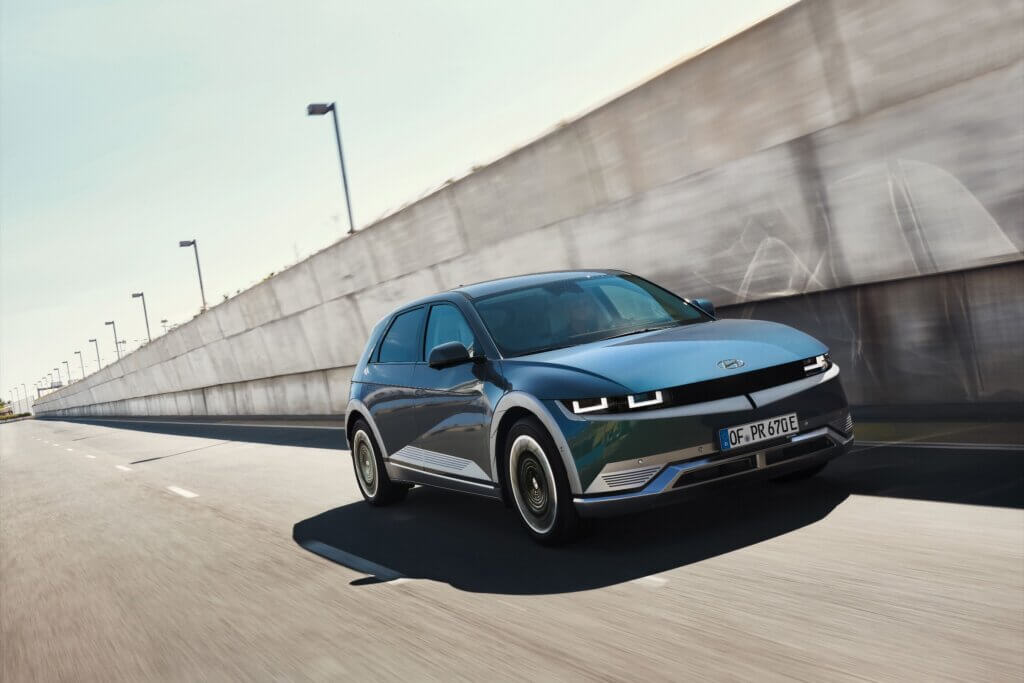
A large investment is required to create a safe structure, and as a result, this is reflected in the slightly higher price of electric cars. Although the design is now done in a virtual environment, additional costs cannot be avoided either. Jon Vanag reminds that the results of the first Chinese electric cars in safety tests were very bad.
These models were very dangerous, and even now Chinese products should be chosen with caution. Of course, these cars are much cheaper, but it is often suspected that the manufacturers’ only goal is quick profit. The attitude of US, Japanese, South Korean and European companies towards safety is completely different – rider protection is an absolute priority.
Jons Vanags, assistant professor of the Faculty of Electric Power and Electronics, Kaunas University of Technology
He adds that electric car platforms help create a circular economy. This means that recycled raw materials, various composite materials and materials from renewable sources are used more.
Various composites are used instead of steel alloys because they are superior in various aspects. They are as plastic as metals, but even stronger, so they do not break in the event of a collision. Various carbon fiber compounds are increasingly being used, such as Kevlar and other materials previously considered exotic.
Jons Vanags, assistant professor of the Faculty of Electric Power and Electronics, Kaunas University of Technology
Fast charging has opened up new possibilities
The biggest advantage in the interior of the new generation of electric cars is the flat floor. The electric motor is usually mounted at the rear, so the front axle is pushed forward as much as possible. This allows you to significantly increase the cabin. In this respect, electric models are clearly superior to internal combustion machines and hybrids. Among mid-size family cars, Tesla Model 3, Hyundai Ioniq 5 and Audi Q4 e-tron stand out with interior capacity. They are all created on specialized platforms.
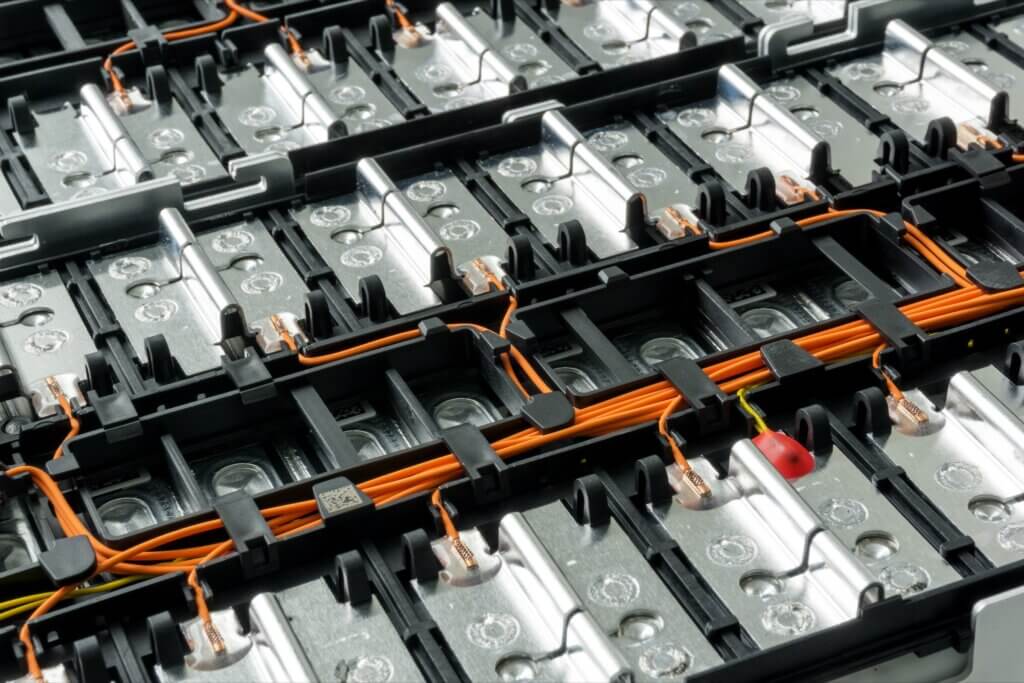
The new generation platforms also stand out with modern charging solutions. Tesla cars have traditionally been unbeatable with charging power of up to 250 kW, but the modern 800-volt systems of Audi, Porsche, Kia and Hyundai have already changed that. For example, the battery of the new Hyundai Ioniq 5 can be charged from 10 to 80 percent in just 18 minutes.
Modern technologies allow you to get enough energy for 100 kilometers in two minutes. However, using devices up to 500 amps for charging creates an additional load on the battery and reduces the number of charging cycles. Therefore, it is important to find an optimal balance between charging speed and battery longevity.
Jons Vanags, assistant professor of the Faculty of Electric Power and Electronics, Kaunas University of Technology